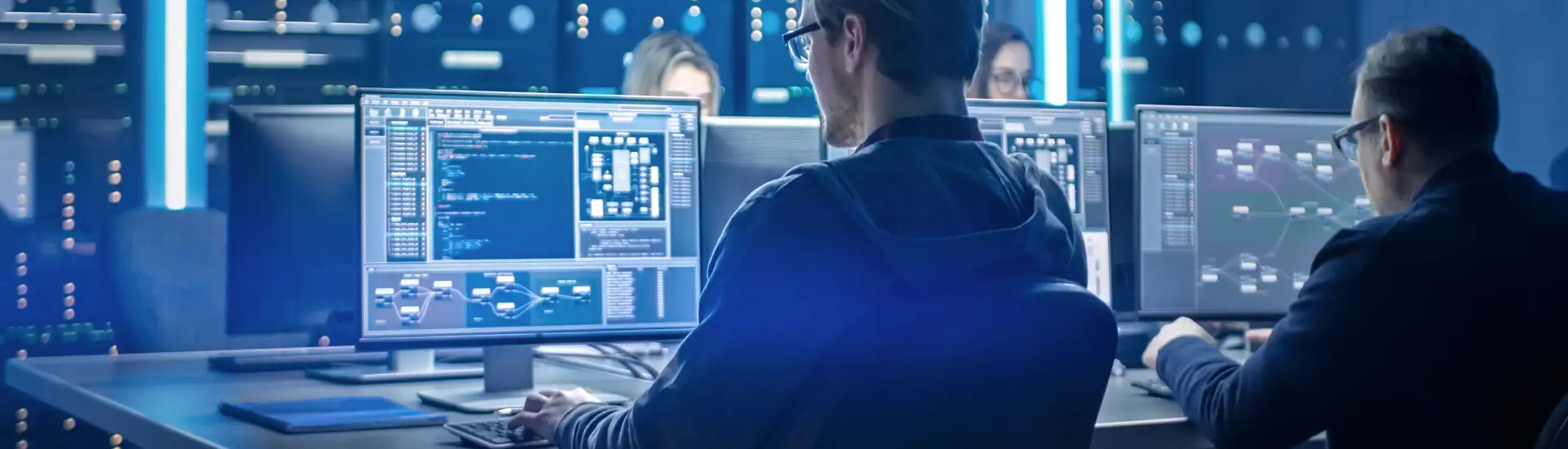
Environmental and process data management
Environmental and process data management systems from the DURAG GROUP are used for the continuous collection, long-term storage, calculation and visualization of environmental and process data. Legally prescribed limit values are monitored, compliance with them is logged and at the same time transferred to the relevant authorities as required.
With more than 40 years of experience in the supply of software and hardware products, we are among the forerunners in the industry in the evaluation of emission and process data. Our system solutions include both continuous emission evaluation systems and innovative predictive emission monitoring systems (PEMS), which use empirical models to determine emissions on the basis of historical and real-time process data.
Our systems can be individually adapted and assembled according to the requirements of the plant and the wishes of the operator. With their modular design, they can also be expanded to include additional components and modules after installation.
Predictive emission monitoring systems (PEMS)
Predictive emission monitoring systems (PEMS) are an innovative and cost-effective approach to continuous emission monitoring as an alternative to continuous emission monitoring systems (CEMS). These software-based systems use process data to enable continuous, real-time monitoring of pollutants such as NOx, SO2, CO, HC or reference variables such as O2.
PEMS use empirical models to determine emissions. They determine the relationship between characteristic process parameters for an emission source and the corresponding emission concentration.
PEMS as a process analysis tool for efficiency and combustion optimization
Turbines, boilers, process heaters and furnaces – just to name a few – are fired with fuels such as natural gas, waste gas, oil, coal, or biomass and require complete combustion to occur. The consumption of these fuels and their emissions can be minimized by optimizing burner efficiency.
Efficiency is directly linked to the flue gas temperature and the amount of oxygen (O2). Complete combustion is a function of oxygen and temperature: If the amount of excess oxygen increases, fuel efficiency, for example of a boiler, decreases. Consequently, reducing excess O2 improves efficiency. However, reducing oxygen can initiate formation of CO. Excess levels of CO indicate incomplete combustion with increased emissions. Monitoring CO with PEMS can ensure that emission concentrations stay within the limit values, with the added value of optimized burner efficiency. PEMS process monitoring of O2 and CO therefore plays a vital role in optimizing combustion plant efficiency and is well accepted by utilities and operators of industrial combustion plants.
As described above, formation of CO is a function of excess O2 in typical combustion applications. However, NOx formation is also influenced by oxygen levels. As excess O2 decreases, NOx decreases while CO and efficiency increase. Excess O2 must be minimized in order to minimize NOx formation and maximize efficiency. However, the amount of CO also needs to be limited. As a result, reducing excess O2 only makes sense until the maximum permissible CO concentration is reached. At this point, an optimized combustion is achieved with a unit operating at the maximum allowable CO rates. This corresponds to the minimum NOx production and maximum efficiency. PEMS will be the tool for continuously monitoring CO, NOx and O2, providing data that alongside other process variables helps to accomplish real-time combustion optimization and to ensure compliance with regulatory requirements.
PEMS can also contribute to managing these tasks significantly less expensively than hardware-based analytical equipment, with the additional benefit of higher uptime and higher data availability. Cost of ownership (CAPEX) can be reduced by as much as 50 percent with operational and maintenance cost (OPEX) typically being only 5-10 percent of an analyzer-based process monitoring system. By virtue of determining the concentrations through correlation with process variables, the operator can immediately see combustion process changes that are the root of concentration changes. When operating a PEMS for units in hazardous areas, OPEX may be up to 20 times less than for ex-proof hardware. Additional benefits are virtually no maintenance requirements, also reducing manpower, as well as no costs for spare parts and consumables.